数控铣床常见主轴伺服系统故障分析(wgb) 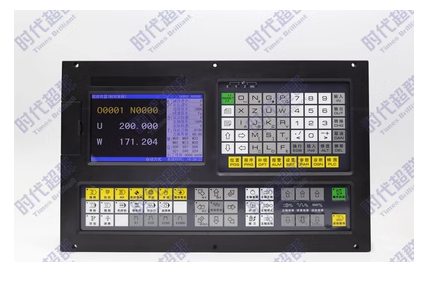 常见主轴伺服系统故障分析。当主轴伺服系统发生故障时,通常有三种表现形式:一是在CRT或操作面板上显示报警内容或报警信息;二是在主轴驱动装置上用报警灯或数码管显示主轴驱动装置的故障;三是主轴工作不正常,但无任何报警信息。主轴伺服系统常见故障如下。 1)外界干扰。由于受到电磁干扰、屏蔽和接地措施不良,主轴转速指令信号或反馈信扰,使主轴驱动出现随机和无规律性的波动。判别有无干扰的方法是,当主轴转速指令为零时,主轴仍往复转动,调整零速平衡和漂移补偿也不能消除故障,则表明存在外界干扰。 2)过载。切削用量过大,或频繁地正、反转变速等均可引起过载报警,具体表现为主轴电动机过热、主轴驱动装置显示过电流等报警。 3)主轴定位抖动。主轴的定向控制(也称主轴定位控制)是将主轴准确停在某一固定位置上,以便在该位置进行刀具交换、精镗退刀及齿轮换档等,以下三种方式可实现主轴准作定向。 ①机械准停控制。由带v形槽的定位盘和定位用的液压缸配合动作。 ②磁性传感器的电气准停控制。发磁体安装在主轴后端,磁性装置安装在主轴箱上,其安装位置决定了主轴的准停点,发磁体和磁性传感器之间的间隙为1.5mm±0.5mm。 ③编码器型的电气准停控制。通过在主轴电动机内安装或在机床主轴上直接安装一个光电脉冲编码器来实现准停控制,准停角度可任意设定。 主轴定向控制实际上是在主轴速度控制基础上增加一个位置控制环。为检测主轴的置,需要采用磁性传感器或位置编码器等检测元件。采用位置编码器作为位置检测元件时,由于安装不方便,一般要通过一对传动比为1:1的齿轮连接。当采用磁性传感器作为位置检测元件时,其磁性元件可直接装在主轴上,而磁性传感头固定在主轴箱体上。为了减少干扰,磁性传感头和放大器之间的连接线需要屏蔽,且两者的连接线越短越好。这两种控制方案各有优缺点,需根据机床的实际情况来选用。产生主轴定位抖动故障的原因为:上述准停均要经过减速的过程,减速或增益等参数设置不当,均可引起定位抖动;采用位置编码器作为检测元件的准停方式时,定位液压缸活塞移动的限位开关失灵,引起定位抖动;采用磁性传感头作为位置检测元件时,发磁体和磁性传感器之间的间隙发生变化或磁性传感器失灵,引起定位抖动。 4)主轴异常噪声及振动。首先要区别异常噪声及振动发生在主轴机械部分还是在电气驱动部分。 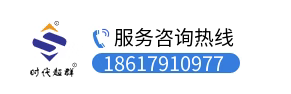 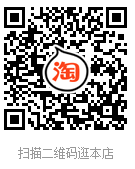
|